
Supply, installation and commissioning of related CSSD associated equipment for most major manufacturers/brands; mainly (but not limited to) sterilizer and washer disinfector.
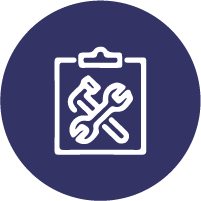
Preventive and corrective maintenance, servicing and repair of related equipment in CSSD environment on per job basis or flexible terms and periods via Planned Preventative Maintenance Service Contracts, to suit customers’ needs.
READ MORE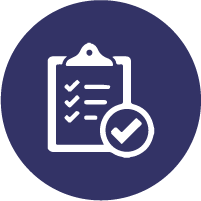
Arrangement and co-ordination work for Department of Occupational Safety & Health (DOSH) / JKKP approval.
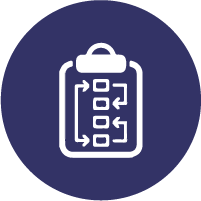
Planning and design of CSSD facilities. Among clients that TISB have serviced in this area include Government Hospitals (new and CSSD upgrading) and private hospitals from Kumpulan Perubatan Johor and Pantai Group.
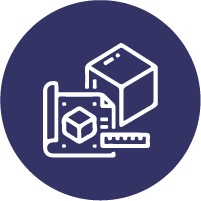
Design and supply of related CSSD associated furniture such as loading/unloading systems, transport trolleys.
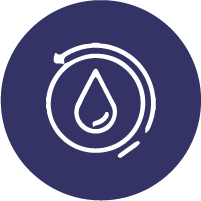
Reverse Osmosis (RO) water treatment systems.
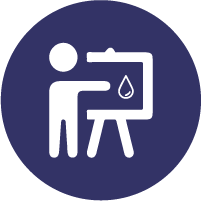
Equipment user training and technical training.
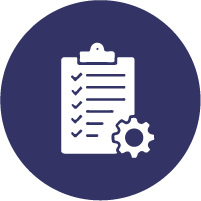
Management of warranty maintenance services on appointment basis.

Steam Quality Test for Dryness, Superheat and Non-Condensable Gas following international standard EN285 criteria.